This is a more complicated decision than it seems at first. Much like choosing between a hydraulic press and a traditional mechanical press, there are a series of trade-offs. Critical attributes to consider when reviewing any press application are control, flexibility and cost.
Control
Process control has become more critical as designers and manufacturers push the limits of new and existing materials. Servo mechanical presses provide a wealth of information on power, speed, force, and position. The servomotors driving the machine provide much of this feedback, using the same data that adjusts speed and power continuously. These adjustments and sensors are what enable servo presses to match preprogrammed process curves well. Servo mechanical presses perform particularly well in applications with high reverse tonnage and materials with significant springback tendencies.
Advanced hydraulic presses use a network of sensors to achieve a similar goal. The force being applied is monitored in the pressurized fluid of each cylinder. Position and speed are measured directly with linear transducers that are accurate within 10 microns. This information is used to manipulate hydraulic valves that control the speed and force independently. The reliance on a fluid, instead of a mechanical connection, can lead to dampened corrections in force or speed with similarly dampened final accuracy. However, at steady forming rates, the difference in accuracy between hydraulic and servo may be only a fractional percent.
Flexibility
Hydraulic presses have long been the default choice for deep forming applications because of their ability to apply full force at any point in the stroke. This enables them to produce parts that would require a servo mechanical press at triple the capacity. Many servo mechanical presses lose 50% of their available tonnage just 1 inch above bottom dead center. The size selection process for a servo press generally mirrors that of a mechanical press, with special attention paid to the forming depth of all the products being manufactured.
Design flexibility of the press can also play a role in choosing the right technology. Servo mechanical presses typically are ordered with a high force per square foot of working area, generally 25 to 50 tons per sq. ft. Hydraulic press designs are easily modified to fit an application, with designs ranging from 1 to 150 tons per sq. ft. Stamping large sheets of thin material on a hydraulic press may require only 5 tons per sq. ft. Having a press that can match the tonnage requirements can improve production rates and reduce costs dramatically.
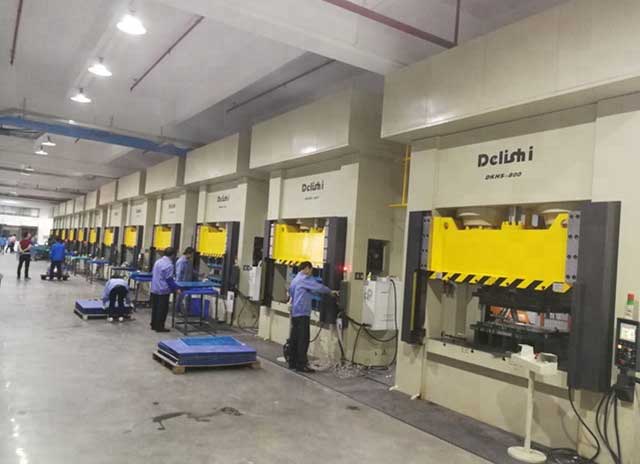
Cost
Servo mechanical press prices have been decreasing as the number of machines being produced has been rising. Generally, though, servo presses still have a higher initial price compared to hydraulic presses, and this cost differential increases at higher capacities.
The servomotor and drive systems are the main reason for these high costs. Hydraulic press pumps and cylinders have a more modest cost, and the price increases that occur as systems grow larger are more moderate too. The total cost of ownership will tend to favor a hydraulic press in many applications, while the lower operating costs of a servo mechanical press may result in cost savings.
Careful Consideration
Hydraulic presses can adapt to produce almost any product cost-effectively and often are the only option for systems with a high force demand early in the stroke. Servo presses represent an evolution in mechanical press technology, opening new opportunities for manufacturers with difficult processes or materials. While they increase the flexibility of the underlying mechanical press design, they still carry many of the same limitations.
Ultimately, the right choice of technology for a press application will vary and should be carefully considered with each new project.