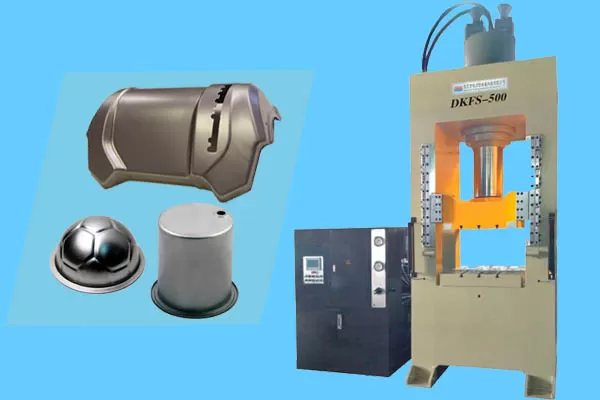
1. Versatility
Wide Range of Applications: Deep drawing hydraulic presses are used in various industries, including automotive, aerospace, electronics, and consumer goods. They can form complex shapes and sizes, making them suitable for producing a wide variety of components.
Material Compatibility: These presses can work with a range of materials, including metals (like steel, aluminum, and copper), plastics, and composites.
2. Precision and Control
High Accuracy: Hydraulic systems offer precise control over the force and speed of the press, ensuring consistent and accurate results. This is crucial for producing high-quality parts with tight tolerances.
Adjustable Parameters: Operators can easily adjust parameters such as pressure, stroke length, and speed to meet specific requirements, allowing for customization and flexibility in production.
3. Efficiency
High Production Rates: Deep drawing hydraulic presses can operate at high speeds, making them efficient for large-scale production. They can also be automated, further increasing productivity.
Reduced Waste: The precision and control offered by hydraulic presses minimize material waste, leading to cost savings and more sustainable manufacturing processes.
4. Durability and Reliability
Robust Construction: Hydraulic presses are built to withstand heavy use and harsh conditions, ensuring long-term reliability and reduced downtime.
Low Maintenance: These machines generally require less maintenance compared to mechanical presses, contributing to lower operational costs.
5. Safety
Controlled Operation: Hydraulic presses operate at controlled speeds and forces, reducing the risk of accidents and ensuring a safer working environment.
Safety Features: Modern hydraulic presses are equipped with various safety features, such as emergency stop buttons, safety guards, and pressure relief valves, to protect operators.
6. Cost-Effectiveness
Lower Initial Investment: Compared to other types of presses, hydraulic presses often have a lower initial cost, making them accessible to a wider range of manufacturers.
Energy Efficiency: Advances in hydraulic technology have led to more energy-efficient systems, reducing operational costs over time.
7. Innovation and Technology Integration
Advanced Controls: Integration with modern control systems, such as CNC (Computer Numerical Control) and PLC (Programmable Logic Controller), allows for more sophisticated and automated operations.
Customization: Manufacturers can customize hydraulic presses to meet specific production needs, enhancing their functionality and application scope.
8. Environmental Considerations
Reduced Noise Pollution: Hydraulic presses generally operate more quietly than mechanical presses, contributing to a better working environment.
Energy Recovery Systems: Some hydraulic presses are equipped with energy recovery systems that recycle energy, further improving their efficiency and reducing environmental impact.
In summary, the popularity of deep drawing hydraulic presses stems from their ability to deliver high-quality, precise, and efficient manufacturing solutions across a wide range of industries. Their versatility, reliability, and cost-effectiveness make them an essential tool in modern production processes.