What is Deep Drawing?
Deep drawing is a sheet metal forming process where a flat sheet metal blank is radially drawn into a forming die by the mechanical action of a punch. The process is characterized by the depth of the drawn part, which is typically greater than its diameter.
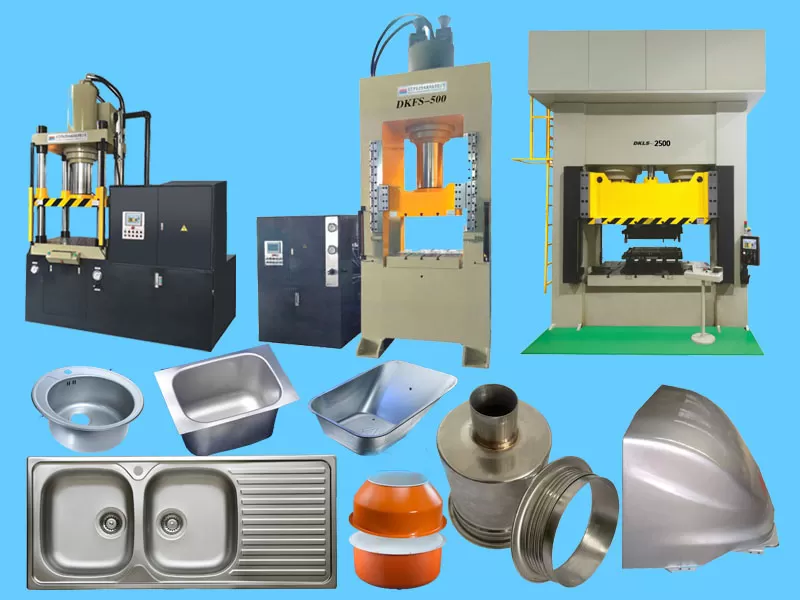
Key Components of Deep Drawing
① Hydraulic Press: Provides the necessary force to draw the metal.
② Punch: The tool that pushes the metal into the die.
③ Die: The cavity that shapes the metal.
④ Blank Holder: Holds the metal blank in place and controls material flow.
Steps in the Deep Drawing Process
1. Material Selection
Choose the appropriate sheet metal material based on the desired properties of the final product. Common materials include:
● Aluminum
● Stainless steel
● Copper
● Brass
2. Blank Preparation
Cut the sheet metal into a blank of the required size and shape. The blank should be slightly larger than the final product to account for material flow and trimming.
3. Lubrication
Apply a lubricant to the blank to reduce friction between the metal and the die. This helps in achieving a smoother surface finish and prolongs the life of the die.
4. Positioning the Blank
Place the blank over the die cavity, ensuring it is centered and properly aligned. The blank holder is then positioned to secure the blank in place.
5. Drawing Process
Activate the hydraulic press to lower the punch into the die cavity. The punch forces the metal blank to take the shape of the die. The hydraulic press provides a controlled and consistent force, which is crucial for achieving uniform wall thickness and avoiding defects.
6. Ejection
Once the drawing process is complete, the punch is retracted, and the formed part is ejected from the die. Ejection can be assisted by air blasts or mechanical ejectors.
7. Trimming and Finishing
Trim any excess material from the drawn part. Additional finishing processes such as deburring, polishing, or coating may be applied to achieve the desired surface quality.
Advantages of Using a Deep Drawing Press
● High Force Capacity: Hydraulic presses can generate significant force, making them suitable for deep drawing large or complex parts.
● Precision Control: Hydraulic systems offer precise control over the speed and force applied, ensuring consistent quality.
● Versatility: Hydraulic presses can be used for a wide range of materials and part sizes.
● Durability: Hydraulic presses are robust and can withstand the high stresses involved in deep drawing.
Common Defects in Deep Drawing and How to Avoid Them
● Wrinkling: Caused by excessive material flow. Use a blank holder with appropriate pressure to control material flow.
● Tearing: Occurs when the material is stretched too thin. Ensure proper lubrication and use a material with adequate ductility.
● Earing: Uneven edges caused by anisotropic material properties. Use materials with uniform grain structure and adjust the blank shape.
● Surface Imperfections: Result from inadequate lubrication or die wear. Regularly maintain and inspect dies, and apply sufficient lubricant.
Applications of Deep Drawing
● Automotive Industry: Manufacturing of car body panels, fuel tanks, and exhaust components.
● Aerospace Industry: Production of aircraft components such as fuselage sections and engine parts.
● Consumer Goods: Making kitchen utensils, sinks, and electronic enclosures.
● Medical Devices: Fabrication of surgical instruments and implantable devices.
Conclusion
The deep drawing process with a hydraulic press is a versatile and efficient method for producing complex, hollow metal parts. By understanding the key steps, advantages, and potential defects, manufacturers can optimize the process to achieve high-quality results. Whether you're in the automotive, aerospace, or consumer goods industry, mastering deep drawing can significantly enhance your production capabilities.
For more detailed insights and specific applications, consult with industry experts or refer to technical manuals and guidelines. Goodsjack offers high quality deep drawing presses with a wide range of output capacity and table sizes that can be completely customized.