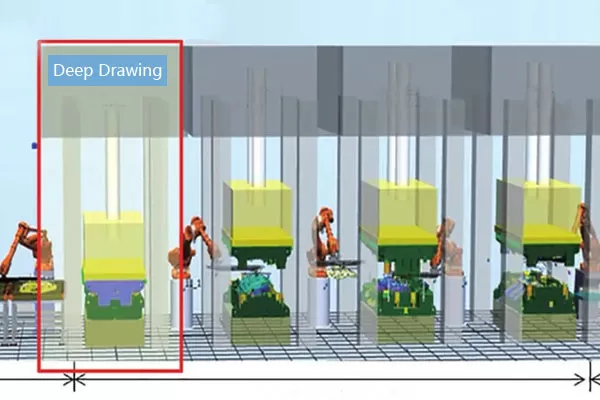
Key Components
1. Hydraulic Press
● High-tonnage capacity (typically 100-5000 tons)
● Programmable hydraulic system with precise pressure control
● CNC controls for repeatable operations
2. Material Handling System
● Automated sheet feeding mechanism
● Blank preparation station (cutting to size)
● Transfer systems between operations
3. Tooling System
● Custom-designed dies and punches
● Quick-change tooling systems for flexible production
● Die cushion systems for wrinkle prevention
4. Ancillary Equipment
● Lubrication systems
● Part ejection mechanisms
● Scrap removal systems
Production Process Flow
1. Blank Preparation
● Coil unwinding and straightening
● Blank cutting to required dimensions
2. Drawing Operation
● First draw (main forming operation)
● Subsequent redrawing operations (if needed)
3. Secondary Operations
● Trimming and piercing
● Flanging and hemming
● Bottom finishing
4. Quality Control
● Dimensional inspection
● Surface quality checks
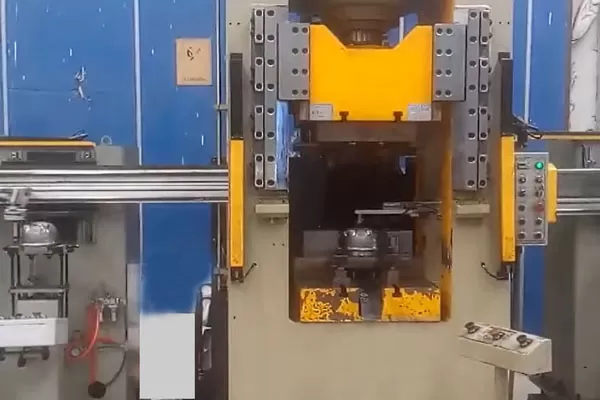
Advantages
High Production Capacity: Capable of producing hundreds to thousands of parts per hour
Precision Forming: Consistent part quality with tight tolerances
Material Efficiency: Minimal scrap generation compared to other forming methods
Versatility: Can handle various materials (steel, aluminum, copper alloys) and thicknesses
Applications
Automotive components (fuel tanks, body panels)
Kitchenware (sinks, pots, pans)
Industrial containers and housings
Aerospace components
Customization Options
Automation Level: From semi-automatic to fully robotic lines
Press Configuration: Single-action, double-action, or triple-action presses
Control Systems: Basic to advanced CNC with IoT connectivity
Safety Systems: Light curtains, interlocks, and pressure monitoring
If you need deep drawing hydraulic press production line, please contact us, best hydraulic press solution will be provided for you.
1. Hydraulic Press
● High-tonnage capacity (typically 100-5000 tons)
● Programmable hydraulic system with precise pressure control
● CNC controls for repeatable operations
2. Material Handling System
● Automated sheet feeding mechanism
● Blank preparation station (cutting to size)
● Transfer systems between operations
3. Tooling System
● Custom-designed dies and punches
● Quick-change tooling systems for flexible production
● Die cushion systems for wrinkle prevention
4. Ancillary Equipment
● Lubrication systems
● Part ejection mechanisms
● Scrap removal systems
Production Process Flow
1. Blank Preparation
● Coil unwinding and straightening
● Blank cutting to required dimensions
2. Drawing Operation
● First draw (main forming operation)
● Subsequent redrawing operations (if needed)
3. Secondary Operations
● Trimming and piercing
● Flanging and hemming
● Bottom finishing
4. Quality Control
● Dimensional inspection
● Surface quality checks
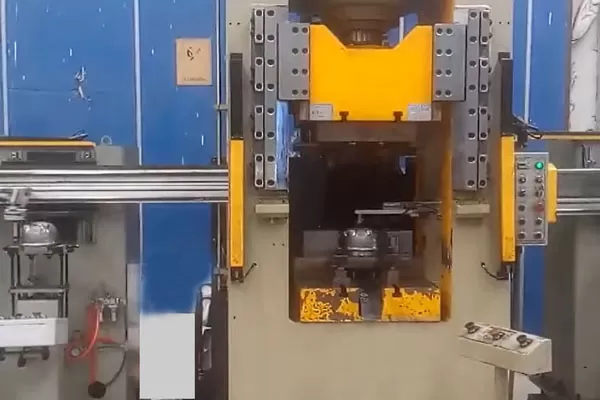
Advantages
High Production Capacity: Capable of producing hundreds to thousands of parts per hour
Precision Forming: Consistent part quality with tight tolerances
Material Efficiency: Minimal scrap generation compared to other forming methods
Versatility: Can handle various materials (steel, aluminum, copper alloys) and thicknesses
Applications
Automotive components (fuel tanks, body panels)
Kitchenware (sinks, pots, pans)
Industrial containers and housings
Aerospace components
Customization Options
Automation Level: From semi-automatic to fully robotic lines
Press Configuration: Single-action, double-action, or triple-action presses
Control Systems: Basic to advanced CNC with IoT connectivity
Safety Systems: Light curtains, interlocks, and pressure monitoring
If you need deep drawing hydraulic press production line, please contact us, best hydraulic press solution will be provided for you.