Deep Drawing Process
The deep draw forming process begins with metal blanks. Typically, single blanks are used in order to facilitate the creation of parts or products with deeper shapes. Sometimes, these metal blanks will be placed on a reel to enable the metal to form efficiently. At each step in the deep drawing process, the metal blank is shaped through pressure applied by a metal die.
Virtually all manufacturing industries have the potential to benefit from deep drawing manufacturing processes. The technique is perhaps most useful for manufacturing small component parts such as electronics relays, solenoids, and assembly housings. Products of all shapes and sizes, however, can be economically created through the process, including items such as aluminum cans, cookware, and kitchen sinks.
Benefits of Deep Drawing
Deep drawing is especially beneficial when producing high volumes, since unit cost decreases considerably as unit count increases: once the tooling and dies have been created, the process can continue with very little downtime or upkeep. Tool construction costs are lower in comparison to similar manufacturing processes, such as progressive die stamping, even in smaller volumes; in these situations deep drawing may also prove the most cost-effective manufacturing solution.
When considering the functionality of the end product, deep drawing poses still more advantages. Specifically, the technique is ideal for products that require significant strength and minimal weight. The process is also recommended for product geometries that are unachievable through other manufacturing techniques.
Deep drawing is perhaps most useful for creating cylindrical objects: a circular metal blank can easily be drawn down into a 3D circular object with a single draw ratio, minimizing both production time and cost. Production of aluminum cans is one example of a popular use of this method.
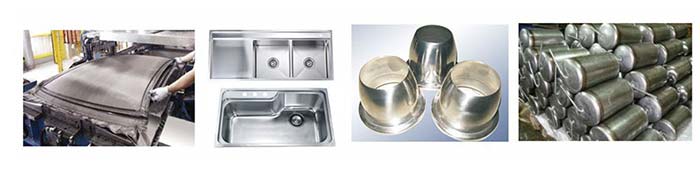
Deep drawing may be a viable production solution for any manufacturing process that requires one or more of the following:
Seamless parts: deep drawn parts are created from a single sheet of metal
Rapid cycle times: large quantities of products are easily manufactured through deep drawing
Complex axi-symmetric geometries: deep drawing delivers exceptional detailing and accuracy
Reduced technical labor: precision deep drawing can deliver similar results as technical labor in quicker time frames
Deep Draw Forming: Other Factors That Affect Cost-Effectiveness Manufacturing costs increase, the subsequent appeal of deep drawing diminishes. More complex products will obviously increase maintenance costs, labor costs, and production costs.