There are many molding processes for carbon fiber composite products. The following are some common molding processes:
Pasting molding process:
Paste the prepreg on the mold by hand, and then cure it. The advantages of this process are simple process equipment, flexible manual processing, and suitable for small batch production. The disadvantages are low production efficiency, poor working conditions, and high labor intensity.
Winding molding process:
After the carbon fiber is impregnated with resin, it is wound on the rotating core mold according to a certain rule, and the glue is cured and formed by heating. This process can arrange the fibers according to a certain rule according to the stress of the product, and give full play to the mechanical properties of carbon fiber. In terms of technology, continuous and mechanized production can be achieved, and the production cycle is short, the production efficiency is high, and the labor intensity is low. It is suitable for the production of cylinders, spheres, and some positive curvature rotating bodies or cylindrical products.
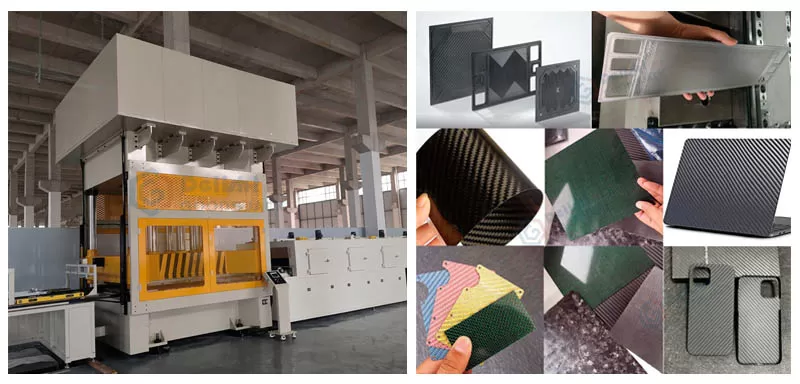
Pultrusion molding process:
After the carbon fiber is impregnated with resin, it is placed in a heated mold for curing. The advantages of this process are high production efficiency and can press out parts with complex shapes and accurate sizes at one time. The disadvantage is that the process equipment is complex and it is not suitable for the preparation of small batches and large sizes. Resin transfer molding (RTM): First, the reinforcement material is made into a preform and placed in a closed mold. Under vacuum and pressure conditions, the resin is injected into the mold and cured. Its advantages are simple process and good product quality; low-pressure injection saves the cost of additional equipment; closed mold operation can keep the working environment clean, and it is easy to realize automation and computer control.
Weaving molding process:
The three-dimensional weaving process is a process in which all the fibers participating in the weaving are arranged in the same direction, and then each fiber bundle is offset in its own direction by an angle to interweave with each other to form a fabric. The composite material using three-dimensional weaving has two major characteristics: integrity and mechanical rationality. It is superior to traditional laminated composite materials in terms of shear strength, impact damage resistance and other properties.
Prepreg molding process: Carbon fiber and resin matrix are pre-impregnated to obtain prepreg. Then the prepreg is laid on the mold according to the design requirements, and the resin matrix is cured by heating and pressurizing to finally obtain a carbon fiber composite material product.
Compression molding process: A molding method in which a carbon fiber composite material prepreg is placed in a mold and the resin matrix is cured by heating and pressurizing. This process has the advantages of high molding pressure, precise temperature control, and high product dimensional accuracy. It is suitable for the production of carbon fiber composite products with complex shapes and high dimensional accuracy requirements.
Injection molding process: a molding method in which the carbon fiber composite prepreg is injected into the mold through an injection machine and the resin matrix is cured by heating and pressurizing. This process has the advantages of high production efficiency, high product dimensional accuracy, and the ability to produce complex-shaped products. It is suitable for the production of large quantities of carbon fiber composite products with complex shapes.