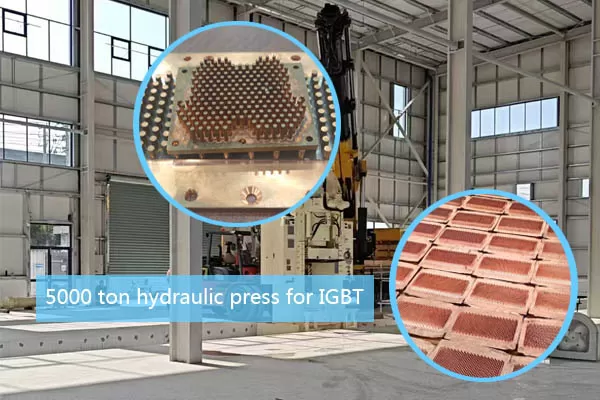
One IGBT industry customer feedback, our 5000 ton hydraulic press is the core equipment for cold extrusion of IGBT copper heat sink.
Analysis of key technologies of 5000-ton hydraulic press in IGBT manufacturing
I. Ultra-heavy cold forging process system
As the core equipment for cold extrusion of IGBT copper heat sink, the 5000 ton hydraulic press has a peak cold forging pressure of up to 1.2GPa, and realizes one-time forming of complex fin structure through room temperature plastic deformation technology. Compared with traditional cutting, this process can increase material utilization by 92%, and reduce the surface roughness of 6063 aluminum alloy substrate to Ra0.4μm, providing atomic-level flat contact surface for IGBT chip. During the cold forging process, metal grains are oriented along the streamline direction to form a natural heat conduction channel, which increases the thermal conductivity of the heat sink by 18%.
2. Innovation and breakthrough in mold materials
For the 1400MPa mold cavity pressure unique to 5,000-ton equipment, the new LG mold steel shows revolutionary advantages:
Toughness is 8-9 times that of traditional DC53 mold steel, and crack resistance is improved by 300%.
Hardness is stable in the HRC54-58 range, and the anti-collapse life exceeds 500,000 forging cycles.
The thermal fatigue resistance coefficient is 2.3 times higher than that of H13 steel, which is suitable for continuous cold forging conditions.
This material, combined with the mold preheating system (150-200℃) of the hydraulic press, effectively solves the problem of mold stress concentration during copper cold extrusion.
3. Intelligent production configuration
5000-ton hydraulic unit integrates multiple intelligent control technologies
Dynamic pressure compensation system: 32 sets of pressure sensors are used to correct the forming curve in real time, and the fin height tolerance is controlled within ±0.03mm.
Mold quick change mechanism: The hydraulic locking device is used to complete the switching of 4 specifications of molds within 5 minutes.
Energy consumption optimization module: Intelligently adjust the main cylinder pressurization rate, and the energy consumption of a single piece is reduced by 42% compared with traditional equipment.
4. Leap in thermodynamic performance
After 50 The 5000-ton cold-forged IGBT heat sink exhibits:
The heat exchange area per unit volume reaches 3000m²/m³, which is 65% higher than that of machined products.
The thermal resistance coefficient is reduced to 0.15℃·cm²/W, and the junction temperature drops by 28℃ under 150A conditions.
The uniformity of the flow channel wall thickness is greater than 98%, eliminating local hot spots caused by welding.
This technology has been successfully applied to the three-electric system of new energy vehicles, making the power density of the 800V high-voltage platform IGBT module exceed 45kW/L8. With the development of silicon carbide devices, the 5000 ton hydraulic press is realizing the interface metallurgical bonding of copper-silicon carbide substrates through in-mold composite forging technology.
Analysis of key technologies of 5000-ton hydraulic press in IGBT manufacturing
I. Ultra-heavy cold forging process system
As the core equipment for cold extrusion of IGBT copper heat sink, the 5000 ton hydraulic press has a peak cold forging pressure of up to 1.2GPa, and realizes one-time forming of complex fin structure through room temperature plastic deformation technology. Compared with traditional cutting, this process can increase material utilization by 92%, and reduce the surface roughness of 6063 aluminum alloy substrate to Ra0.4μm, providing atomic-level flat contact surface for IGBT chip. During the cold forging process, metal grains are oriented along the streamline direction to form a natural heat conduction channel, which increases the thermal conductivity of the heat sink by 18%.
2. Innovation and breakthrough in mold materials
For the 1400MPa mold cavity pressure unique to 5,000-ton equipment, the new LG mold steel shows revolutionary advantages:
Toughness is 8-9 times that of traditional DC53 mold steel, and crack resistance is improved by 300%.
Hardness is stable in the HRC54-58 range, and the anti-collapse life exceeds 500,000 forging cycles.
The thermal fatigue resistance coefficient is 2.3 times higher than that of H13 steel, which is suitable for continuous cold forging conditions.
This material, combined with the mold preheating system (150-200℃) of the hydraulic press, effectively solves the problem of mold stress concentration during copper cold extrusion.
3. Intelligent production configuration
5000-ton hydraulic unit integrates multiple intelligent control technologies
Dynamic pressure compensation system: 32 sets of pressure sensors are used to correct the forming curve in real time, and the fin height tolerance is controlled within ±0.03mm.
Mold quick change mechanism: The hydraulic locking device is used to complete the switching of 4 specifications of molds within 5 minutes.
Energy consumption optimization module: Intelligently adjust the main cylinder pressurization rate, and the energy consumption of a single piece is reduced by 42% compared with traditional equipment.
4. Leap in thermodynamic performance
After 50 The 5000-ton cold-forged IGBT heat sink exhibits:
The heat exchange area per unit volume reaches 3000m²/m³, which is 65% higher than that of machined products.
The thermal resistance coefficient is reduced to 0.15℃·cm²/W, and the junction temperature drops by 28℃ under 150A conditions.
The uniformity of the flow channel wall thickness is greater than 98%, eliminating local hot spots caused by welding.
This technology has been successfully applied to the three-electric system of new energy vehicles, making the power density of the 800V high-voltage platform IGBT module exceed 45kW/L8. With the development of silicon carbide devices, the 5000 ton hydraulic press is realizing the interface metallurgical bonding of copper-silicon carbide substrates through in-mold composite forging technology.