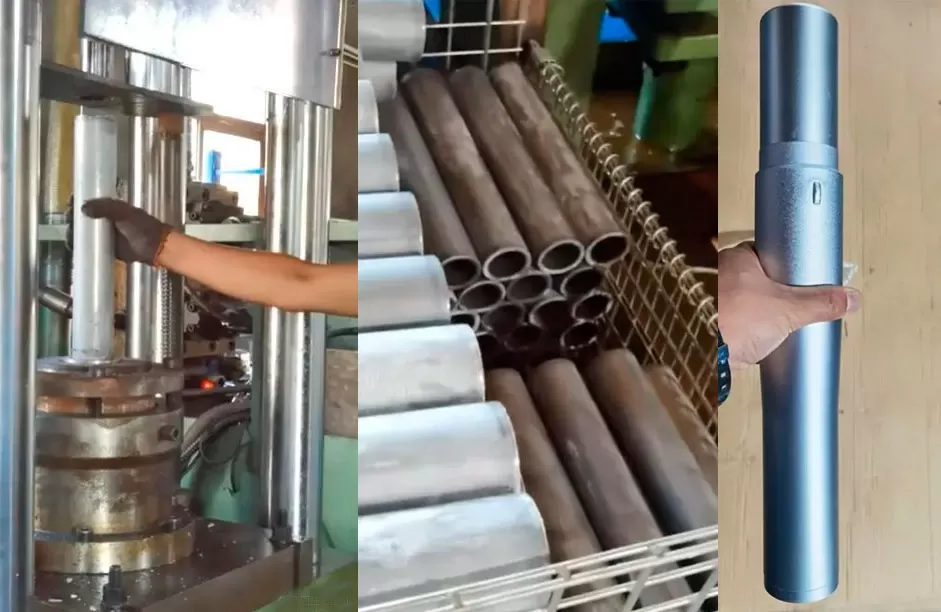
The technical process of cold extrusion of automobile shock absorber oil storage cylinder by hydraulic cold extrusion press is mainly divided into several steps:
1. Processing analysis: First, it is necessary to analyze the parts of the automobile shock absorber oil storage tank to be processed, and analyze the parameters of the material, structure and size of the parts to determine the design parameters of extrusion processing.
2. Manufacture of molds: According to the results of the above analysis, manufacture extrusion molds and polish the surface of the molds to make the deep-level processing precision meet the requirements.
3. Prepare the extrusion material: When preparing the extrusion material, the shape of the mold needs to be considered to ensure that the extrusion material can perfectly fit the surface of the mold.
4. Cycle before processing: Before processing, temperature cycle is required to heat-treat the extruded material to the required temperature during extrusion.
5. Extrusion processing: Put the extrusion material into the extrusion die, and then extrude the parts through the automobile shock absorber accessories extrusion hydraulic press - 800 tons of 1000 extrusion presses to form extrusion parts.
6. Removal of residues: remove the residues of the extrusion die to ensure the surface finish.
7. Performance testing: Test the performance parameters such as surface roughness and dimensional accuracy of the extruded parts to ensure the quality of the parts.